Recirculating Aquaculture Tank Production Systems An Overview of Critical Considerations
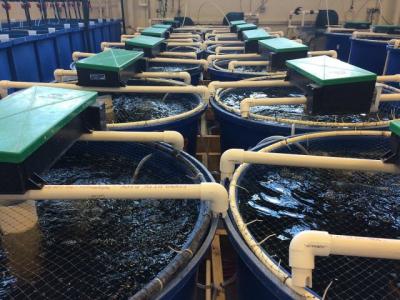
Traditional aquaculture production in ponds requires large quantities of water. Approximately 1 million gallons of water per acre are required to fill a pond and an equivalent volume is required to compensate for evaporation and seepage during the year. Assuming an annual pond yield of 5,000 pounds of fish per acre, approximately 100 gallons of water are required per pound of fish production. In many areas of the United States, traditional aquaculture in ponds is not possible because of limited water supplies or an absence of suitable land for pond construction.
Recirculating aquaculture production systems may offer an alternative to pond aquaculture technology. Through water treatment and reuse, recirculating systems use a fraction of the water required by ponds to produce similar yields. Because recirculating systems usually use tanks for aquaculture production, substantially less land is required.
Aquatic crop production in tanks and raceways where the environment is controlled through water treatment and recirculation has been studied for decades. Although these technologies have been costly, claims of impressive yields with year-round production in locations close to major markets and with extremely little water usage have attracted the interest of prospective aquaculturists. In recent years, a variety of production facilities that use recirculating technology have been built. Results have been mixed. While there have been some notable large-scale business failures in this sector, numerous small- to medium-scale efforts continue production.
Prospective aquaculturists and investors need to be aware of the basic technical and economic risks involved in this type of aquaculture production technology. This fact sheet and others in this series are designed to provide basic information on recirculating aquaculture technology.
Critical production considerations
All aquaculture production systems must provide a suitable environment to promote the growth of the aquatic crop. Critical environmental parameters include the concentrations of dissolved oxygen, un-ionized ammonia-nitrogen, nitrite-nitrogen, and carbon dioxide in the water of the culture system. Nitrate concentration, pH, and alkalinity levels within the system are also important. To produce fish in a costeffective manner, aquaculture production systems must maintain good water quality during periods of rapid fish growth. To ensure such growth, fish are fed high-protein pelleted diets at rates ranging from 1.5 to 15 percent of their body weight per day depending upon their size and species (15 percent for juveniles, 1.5 percent for market size).
Feeding rate, feed composition, fish metabolic rate and the quantity of wasted feed affect tank water quality. As pelleted feeds are introduced to the fish, they are either consumed or left to decompose within the system. The byproducts of fish metabolism include carbon dioxide, ammonia-nitrogen, and fecal solids. If uneaten feeds and metabolic byproducts are left within the culture system, they will generate additional carbon dioxide and ammonia-nitrogen, reduce the oxygen content of the water, and have a direct detrimental impact on the health of the cultured product.
In aquaculture ponds, proper environmental conditions are maintained by balancing the inputs of feed with the assimilative capacity of the pond. The ponds natural biological productivity (algae, higher plants, zooplankton and bacteria) serves as a biological filter that processes the wastes. As pond production intensifies and feed rates increase, supplemental and/or emergency aeration are required. At higher rates of feeding, water must be exchanged to maintain good water quality.
The carrying capacity of ponds with supplemental aeration is generally considered to be 5,000 to 7,000 pounds of fish per acre (0.005 to 0.007 pound of fish per gallon of pond water). The carrying capacity of tank systems must be high to provide for cost-effective fish production because of the higher initial capital costs of tanks compared to earthen ponds. Because of this expense and the limited capacity of the natural biological filtration of a tank, the producer must rely upon the flow of water through the tanks to wash out the waste by-products. Additionally, the oxygen concentration within the tank must be maintained through continuous aeration, either with atmospheric oxygen (air) or pure gaseous oxygen.
The rate of water exchange required to maintain good water quality in tanks is best described using an example. Assume that a 5,000-gallon production tank is to be maintained at a culture density of 0.5 pound of fish per gallon of tank volume. If the 2,500 pounds of fish are fed a 32% protein feed at a rate of 1.5 percent of their body weight per day, then 37.5 pounds of feed would produce approximately 1.1 pounds of ammonia-nitrogen per day. (Approximately 3 percent of the feed becomes ammonia-nitrogen.) Additionally, if the ammonianitrogen concentration in the tank is to be maintained at 1.0 mg/l, then a mass balance calculation on ammonia-nitrogen indicates that the required flow rate of new water through the tank would be approximately 5,600 gallons per hour (93 gpm) to maintain the specified ammonia-nitrogen concentration. Even at this high flow rate, the system also would require aeration to supplement the oxygen added by the new water.
Recirculating systems design
Recirculating production technology is most often used in tank systems because sufficient water is not available on site to wash fish wastes out of production tanks in a flow-through configuration or production system that uses water only once. In most cases, a flow-through requirement of nearly 100 gallons per minute to maintain one production tank would severely limit production capacity. By recirculating tank water through a water treatment system that removes ammonia and other waste products, the same effect is achieved as with the flow-through configuration. The efficiency with which the treatment system removes ammonia from the system, the ammonia production rate, and the desired concentration of ammonia-nitrogen within the tank determine the recirculating flow rate from the tank to the treatment unit. Using the example outlined above, if a treatment system removes 50 percent of the ammonia-nitrogen in the water on a single pass, then the flow rate from the tank would need to be twice the flow required if fresh water were used to flush the tank (93 gpm/0.5 = 186 gpm).
A key to successful recirculating production systems is the use of cost-effective water treatment system components. All recirculating production systems remove waste solids, oxidize ammonia and nitrite-nitrogen, remove carbon dioxide, and aerate or oxygenate the water before returning it to the fish tank (see Fig. 1). More intensive systems or systems culturing sensitive species may require additional treatment processes such as fine solids removal, dissolved organics removal, or some form of disinfection.
Waste solids constraints
Pelleted feeds used in aquaculture production consist of protein, carbohydrates, fat, minerals and water. The portion not assimilated by the fish is excreted as a highly organic waste (fecal solids). When broken down by bacteria within the system, fecal solids and uneaten feed will consume dissolved oxygen and generate ammonia-nitrogen. For this reason, waste solids should be removed from the system as quickly as possible. Waste solids can be classified into four categories: settleable, suspended, floatable and dissolved solids. In recirculating systems, the first two are of primary concern. Dissolved organic solids can become a problem in systems with very little water exchange.
Settleable solids control:
Settleable solids are generally the easiest of the four categories to deal with and should be removed from the tank and filtration components as rapidly as possible. Settleable solids are those that will generally settle out of the water within 1 hour under still conditions. Settleable solids can be removed as they accumulate on the tank bottom through proper placement of drains, or they can be kept in suspension with continuous agitation and removed with a sedimentation tank (clarifier), mechanical filter (granular or screen), or swirl separator. The sedimentation and swirl separator processes can be enhanced by adding steep incline tubes (tubesettlers) in the sedimentation tank to reduce flow turbulence and promote uniform flow distribution.
Figure 1. Required unit processes and some typical components used in recirculating aquaculture production systems.
Suspended solids control:
From an aquacultural engineering point of view, the difference between suspended solids and settleable solids is a practical one. Suspended solids will not settle to the bottom of the fish culture tank and cannot be removed easily in conventional settling basins. Suspended solids are not always dealt with adequately in a recirculating production system. If not removed, suspended solids can significantly limit the amount of fish that can be grown in the system and can irritate the gills of fish. The most popular treatment method for removing suspended solids generally involves some form of mechanical filtration. The two types of mechanical filtration most commonly used are screen filtration and granular media filtration (sand or pelleted media). For more information on these devices see SRAC 453, Recirculating Aquaculture Tank Production Systems: AReview of Component Options.
Fine and dissolved solids control:
Fine suspended solids (< 30 micrometers) have been shown to contribute more than 50 percent of the total suspended solids in a recirculating system. Fine suspended solids increase the oxygen demand of the system and cause gill irritation and damage in finfish. Dissolved organic solids (protein) can contribute significantly to the oxygen demand of the total system.
Fine and dissolved solids cannot be easily or economically removed by sedimentation or mechanical filtration technology. Foam fractionation (also referred to as protein skimming) is successful in removing these solids from recirculating tank systems. Foam fractionation, as employed in aquaculture, is a process of introducing air bubbles at the bottom of a closed column of water that creates foam at the top air/water interface. As the bubbles rise through the water column, solid particles attach to the bubbles surfaces, forming the foam at the top of the column. The foam build-up is then channelled out of the fractionation unit to a waste collection tank. Solids concentration in the waste tank can be five times higher than that of the culture tank. Although the efficiency of foam fractionation is subject to the chemical properties of the water, the process generally can be used to significantly reduce water turbidity and oxygen demand of the culture system.
Nitrogen constraints
Total ammonia-nitrogen (TAN), consisting of un-ionized ammonia (NH3) and ionized ammonia (NH4+), is a by-product of protein metabolism. TAN is excreted from the gills of fish as they assimilate feed and is produced when bacteria decompose organic waste solids within the system. The unionized form of ammonia-nitrogen is extremely toxic to most fish. The fraction of TAN in the un-ionized form is dependent upon the pH and temperature of the water. At a pH of 7.0, most of the TAN is in the ionized form, while at a pH of 8.75 up to 30 percent of TAN is in the un-ionized form. While the lethal concentration of ammonia-nitrogen for many species has been established, the sub-lethal effects of ammonia-nitrogen have not been well defined. Reduction in growth rates may be the most important sub-lethal effect. In general, the concentration of un-ionized ammonia-nitrogen in tanks should not exceed 0.05 mg/l.
Nitrite-nitrogen (NO2- ) is a product of the oxidation of ammonianitrogen. Nitrifying bacteria (Nitrosomonas) in the production system utilize ammonia-nitrogen as an energy source for growth and produce nitrite-nitrogen as a by-product. These bacteria are the basis for biological filtration. The nitrifying bacteria grow on the surface of the biofilter substrate although all tank production system components will have nitrifying bacteria present to some extent. While nitrite-nitrogen is not as toxic as ammonia-nitrogen, it is harmful to aquatic species and must be controlled within the tank.
Nitrite-nitrogen binds with hemoglobin to produce methemoglobin. Methemoglobin is not capable of binding and transporting oxygen and the affected fish become starved for oxygen. The toxicity of nitrite-nitrogen is species specific. However, a common practice for reducing nitrite-nitrogen toxicity is to increase the chloride concentration of the culture water. Maintaining a chloride to nitrite-nitrogen ratio of 10:1 generally will protect against methemoglobin build-up and nitrite-nitrogen toxicity. Fortunately, Nitrobacter bacteria, which also are present in most biological filters, utilize nitritenitrogen as an energy source and produce nitrate as a by-product. In a recirculating system with a mature biofilter, nitrite-nitrogen concentrations should not exceed 10 mg/l for long periods of time and in most cases should remain below 1 mg/l.
Nitrates are not generally of great concern to the aquaculturist. Studies have shown that aquatic species can tolerate extremely high levels (> 200 mg/l) of nitrate-nitrogen in production systems. Nitrate-nitrogen concentrations do not generally reach such high levels in recirculating systems. Nitrate-nitrogen is either flushed from a system during system maintenance operations (such as settled solids removal or filter backwashing), or denitrification occurs within a treatment system component such as a settling tank. Denitrification occurs when anaerobic bacteria metabolize nitratenitrogen to produce nitrogen gas that is released to the atmosphere during the aeration process. For more information on the effects of water quality on fish production, see SRAC 452, Recirculating Aquaculture Tank Production Systems: Management of Recirculating Systems.
Ammonia and nitrite-nitrogen control:
Controlling the concentration of un-ionized ammonianitrogen (NH3) in the culture tank is a primary objective of recirculating treatment system design. Ammonia-nitrogen must be removed from the culture tank at a rate equal to the rate of production to maintain a safe concentration. While there are a number of technologies available for removing ammonia-nitrogen from water, biological filtration is the most widely used. In biological filtration (also referred to as biofiltration), there is a substrate with a large surface area where nitrifying bacteria can attach and grow. As previously noted, ammonia and nitrite-nitrogen in the recycle stream are oxidized to nitrite and nitrate-nitrogen by Nitrosomonas and Nitrobacter bacteria, respectively. Gravel, sand, plastic beads, plastic rings, plastic tubes, and plastic plates are common biofiltration substrates. The configuration of the substrate and the manner in which it comes into contact with wastewater define the water treatment characteristics of the biological filtration unit. The most common configurations for biological filters include rotating biological contactors (RBC), fixed film reactors, expandable media filters, and mixed bed reactors. For more information on biological filters and components see SRAC 453, Recirculating Aquaculture Tank Production Systems: AReview of Component Options.
pH and alkalinity constraints
The measure of the hydrogen ion (H+) concentration, or pH, in water indicates the degree to which water is either acidic or basic. The pH of water affects many other water quality parameters and the rates of many biological and chemical processes. Thus, pH is considered an important parameter to be monitored and controlled in recirculating aquaculture systems. Alkalinity is a measure of the waters capacity to neutralize acidity (hydrogen ions). Bicarbonate (HCO3-) and carbonate (CO3-) are the predominant bases or sources of alkalinity in most waters. Highly alkaline waters are more strongly buffered against pH change than less alkaline waters.
Nitrification is an acid-producing process. As ammonia-nitrogen is transformed to nitrate-nitrogen by nitrifying bacteria, hydrogen ions are produced. As hydrogen ions combine with bases such as hydroxide (OH-), carbonate and bicarbonate, alkalinity is consumed and the pH decreases. Levels of pH below 4.5 are dangerous to fish; a pH below 7.0 will reduce the activity of nitrifying bacteria. If the source water for a recirculating system is low in alkalinity, then pH and alkalinity should be monitored and alkalinity must be maintained with additions of bases. Some bases commonly used include hydrated lime [Ca(OH)2] quick lime (CaO), and sodium bicarbonate (NaHCO3).
Dissolved gas constraints
Although ammonia-nitrogen build-up can severely limit a recirculating systems carrying capacity, maintaining adequate dissolved oxygen (DO) concentrations in the culture tank and filter system also is of critical importance. In most cases, a systems ability to add dissolved oxygen to water will become the first limiting factor in a systems fish carrying capacity. To maintain adequate DO levels in the culture tank, oxygen must be added to the tank at a rate equal to that of the rate of consumption by fish and bacteria. The consumption rate of dissolved oxygen in a recirculating system is difficult to calculate, yet an estimate is essential for proper system design. The overall rate of oxygen consumption for a system is the sum of the respiration rate of the fish, the oxygen demand of bacteria breaking down organic wastes and uneaten food (also referred to as Biochemical Oxygen Demand or BOD), and the oxygen demand of nitrifying bacteria in the filter. The amount of oxygen required by the system is largely dictated by the length of time waste solids remain within the system and the biofilter configuration. In systems with non-submerged biofilters, where solids are removed quickly, as little as 0.3 pound of oxygen can be consumed for every pound of feed added. In systems with submerged biological filters, where solids are retained within the system between backwashings of solid-removing filters, as much as 0.75 pound of oxygen will be consumed for every pound of feed added.
Carbon dioxide (CO2) is a byproduct of fish and bacterial respiration and it can accumulate within recirculating systems. Elevated carbon dioxide concentrations in the water are not highly toxic to fish when sufficient dissolved oxygen is present. However, for most species, free carbon dioxide concentrations in the culture tank should be maintained at less than 20 mg/l to maintain good growing conditions.
The build-up of dissolved nitrogen gas is rarely a problem in warm water aquaculture systems. However, caution is advised when pressurized aeration or oxygenation systems are used because atmospheric nitrogen can become supersaturated in water if air is entrained into the pressurized flow stream. Aquatic organisms subjected to elevated concentrations of dissolved nitrogen gas can develop gas bubbles in their circulatory systems and die.
Maintaining adequate dissolved oxygen levels and minimizing carbon dioxide concentrations in the culture tank cannot be overlooked in recirculating system design. In a typical intensively loaded recirculating system, aeration or oxygenation system failure can lead to a total loss of the fish crop in 1/2 hour or less.
Aeration and Degassing:
The addition of atmospheric oxygen to water or the release of excess carbon dioxide from water can be accomplished in recirculating systems through a variety of devices such as air diffusers, surface agitators, and pressurized or nonpressurized packed columns. System aeration is commonly carried out in the culture tanks, although this is not a particularly good place to add dissolved oxygen. This is because the oxygen transfer efficiency of aerators drops as the concentration of dissolved oxygen increases to near saturation levels in the tank water. Because saturated conditions are desirable in the culture tank, aeration in this location is extremely inefficient.
In recirculating systems, a better place to aerate and degas water is in the recycled flow-stream just prior to re-entry into the culture tank. At this location, in systems using submerged biological filtration, the concentration of dissolved oxygen should be at its lowest and carbon dioxide concentration will be at its highest. Packed column aerators (PCAs) are an effective and simple means of aerating water that is already in a flow-stream. In a PCA, water low in oxygen is introduced into a small tower filled with plastic medium. Aperforated plate or spray nozzle evenly distributes the incoming water over the medium. The packed column is operated under non-flooded conditions so that air exchange through the tower is maintained. If the PCAis to be used for carbon dioxide stripping, a low pressure air blower will be required to provide a large quantity of air flow through the packed medium.
A number of recirculating system designs use air-lift pumps (vertical pipes with air injection) to recycle water through treatment processes and back to the culture tank. Air lifts agitate the water with air bubbles in the process and remove CO2 and add dissolved oxygen.
Pure Oxygen Injection:
In intensive production systems, the rate of oxygen consumption by the fish and bacteria may exceed the capabilities of typical aeration equipment to diffuse atmospheric oxygen into the water. In these cases, pure gaseous oxygen diffusion is used to increase the rate of oxygen addition and allow for a higher oxygen utilization rate. The saturation concentration of atmospheric oxygen in water rarely exceeds 8.75 mg/l in warm water applications (> 20o C). When pure oxygen is used with gas diffusion systems, the saturation concentration of oxygen in water is increased nearly five fold to 43 mg/l at standard atmospheric pressure. This condition allows for more rapid transfer of oxygen into water even when the ambient tank dissolved oxygen concentration is maintained close to atmospheric saturation (> 7 mg/l).
Ameasure of success in using pure oxygen in aquaculture is the oxygen absorption efficiency of the injection or diffusion equipment. The absorption efficiency is defined as the ratio of the weight of oxygen absorbed by the water to the weight of oxygen applied through the diffusion or injection equipment. Properly designed oxygen diffusion devices can produce an oxygen absorption efficiency of more than 90 percent. However, as with tank aeration (with air), the culture tank is not the best location for oxygen diffusion with common air stone diffusers. Because of the short contact time of bubbles rising through a shallow (< 6 feet) water column in tanks, air stone diffusers have oxygen absorption efficiencies of not greater than 40 percent. Efficient oxygen injection systems are designed to maximize both the oxygen/water contact area and time. This can be achieved through the use of a counter-current contact column, a closed packed-column contact unit, a u-tube column or a downflow bubble contactor. For more information on aeration and oxygenation equipment see SRAC 453, Recirculating Aquaculture Tank Production Systems: Component Options.
Other production considerations
There have not been many welldocumented successes in largescale fish production in recirculating systems. Most reports of successful production have been from producers who supply fish live or on ice to local niche markets.
These high-priced markets appear to be necessary for financial success due to the high cost of fish production in recirculating systems. In fact, the variable costs (feed, fingerling, electricity and labor) of producing fish in recirculating systems is not much different than other production methods. Where pond culture methods require a great deal of electricity (at least 1 kW per acre of pond) for aeration during the summer months, recirculating systems have a steady electrical load over the entire year. While it may appear that recirculating systems require more labor in system upkeep and maintenance than ponds, when the long hours of nightly labor for checking oxygen in ponds and moving emergency aerators and harvest effort are considered, the difference is minimal. Recirculating systems can actually have an advantage in reducing feed costs. Tank production systems generally yield better feed conversion ratios than pond systems.
Why, then, are production costs generally higher for recirculating systems? The answer usually can be found when comparing the capital cost of these systems.
Comparing the investment costs of recirculating systems with other production methods is critical in making an informed economic evaluation. Construction costs of pond production systems in the Southeast are approximately 90 cents per pound of annual production. Recirculating systems, on the other hand, cost between $1 and $4 per pound of annual production. A$1 increase in investment cost per pound of annual production can add more than 10 cents per pound to the production cost of fish.
Given these conditions, producers using recirculating technology generally do not attempt to compete in the same markets as pond producers. However, in specialty high-value niche markets, such as gourmet foods, tropical or ornamental fish, or year-round supply of fresh product, recirculating system products are finding a place. The key to niche market success is to identify the market size and meet commitments before market expansion. In most cases, niche markets will limit the size of the production units.
Before investing in recirculating systems technology, the prospective aquaculturist should visit a commercial system and learn as much about the technology as possible. As in all aquaculture enterprises, the decision to begin production and the size of the production unit one chooses should be based on the market.
Related news
Tools

Phối trộn thức ăn chăn nuôi

Pha dung dịch thủy canh

Định mức cho tôm ăn

Phối trộn phân bón NPK

Xác định tỷ lệ tôm sống

Chuyển đổi đơn vị phân bón

Xác định công suất sục khí

Chuyển đổi đơn vị tôm

Tính diện tích nhà kính

Tính thể tích ao