A Guide to Recirculation Aquaculture - Part 8
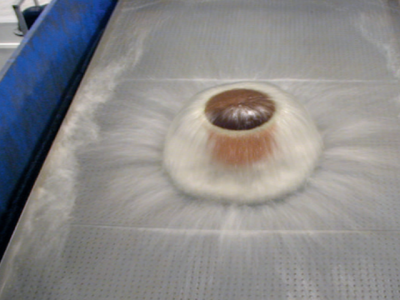
Chapter 5: Running a recirculation system
Figure 5.1 Water quality and flow in filters and fish tanks should be examined visually and frequently. Water is distributed over the top plate of a traditional trickling filter (degasser) and distributed evenly through the plate holes down through the filter media.
Moving from traditional fish farming to recirculation significantly changes the daily routines and skills necessary for managing the farm. The fish farmer has now become a manager of both fish and water. The task of managing the water and maintaining its quality has become just as important, if not more so, than the job of looking after the fish. The traditional pattern of doing the daily job on a traditional flow-through farm has changed into fine tuning a machine that runs constantly 24 hours a day. Automatic surveillance of the whole system ensures that the farmer has access to information on the farm at all times, and an alarm system will call if there is an emergency.
Routines and procedures
The most important routines and working procedures are listed below. Many more details will occur in practice, but the overall pattern should be clear. It is essential to make a list with all the routines to be checked each day, and also lists for checking at longer intervals.
Daily or weekly:
• Visually examine the behaviour of the fish
• Visually examine the water quality (transparency/turbidity) • Check hydrodynamics (flow) in tanks
• Check distribution of feed from feeding machines
• Remove and register dead fish
• Flush outlet from tanks if fitted with stand-pipes
• Wipe off membrane of oxygen probes
• Registration of actual oxygen concentration in tanks
• Check water levels in pump sumps
• Check nozzles spraying on mechanical filters
• Registration of temperature
• Make tests of ammonia, nitrite, nitrate, pH
• Registration of volume of new water used
• Check pressure in oxygen cones
• Check NaOH or lime for pH regulation
• Control that UV-lights are working
• Register electricity (kWh) used
• Read information from colleagues on the message board
• Make sure the alarm system is switched on before leaving the farm.
Weekly or monthly:
• Clean the biofilters according to the manual
• Drain condense water from compressor
• Check water level in buffer tank
• Check amount of remaining O2 in oxygen tank • Calibration of pH-meter
• Calibration of feeders
• Calibrate O2 probes in fish tanks and system
• Check alarms – make alarm tests
• Check that emergency oxygen works in all tanks
• Check all pumps and motors for failure or dissonance
• Check generators and make a test-start
• Check that ventilators for trickling filters are running
• Grease the bearings of mechanical filters
• Rinse spraybar nozzles on mechanical filters
• Search for “dead water” in system and take precautions • Check filter sumps - no sludge must be observed.
Figure 5.2 Oxygen generator. Control and service of special installations must be taken care of.
6-12 months:
• Clean UV sterilizer, change lamps yearly
• Change oil and oil-filters and air-filter on compressor • Check if the cooling towers are clean inside
• Check if degasser is dirty and clean if necessary
• Clean biofilter thoroughly if necessary
• Service the oxygen probes
• Change spraybar nozzles in mechanical filters
• Change filter plates in mechanical filters.
Water quality
Managing the recirculation system requires continuous registration and adjusting to reach a perfect environment for the fish cultured. For each parameter concerned there are certain margins for what is biologically acceptable. Throughout the production cycle each section of the farm should if possible be shut down and started up again for a new batch of fish. Changes in production affect the system as a whole, but especially the biofilter is sensitive to dry outs or other alterations. In figure 5.3 the effect on the concentration of nitrogen compounds leaving a newly started biofilter can be observed. Fluctuations will occur for many other parameters of which the most important can be seen in figure 5.4. In some situations parameters may raise to levels which are unfavourable or even toxic to fish. However, it is impossible to give exact data on these levels as the toxicity depends on different things, such as fish species, temperature and pH. The fish will most often adapt to the environmental conditions of the system and thus tolerate higher levels of certain parameters, such as carbon dioxide, nitrate or nitrite. Most important is to avoid sudden changes in the physical and chemical parameters of the water.
Figure 5.3 Fluctuations in the concentration of different nitrogen compounds from start-up of a biofilter.
Figure 5.4 Preferable levels for diff erent physical and chemical water quality parameters in a recirculati on system.
The toxicity of the nitrite peak can be eliminated by adding salt to the system. A salt concentration in the water of just 0.3 o/oo (ppm) is sufficient to inhibit the the toxicity of nitrite. Suggested levels for different physical and chemical water quality parameters in a recirculation system.
Biofilter maintenance
The biofilter must be working at optimal conditions all times in order to secure a high and stable water quality in the system. The following is an example of procedures for maintenance of the biofilter.
Figure 5.5 Principle drawing of biofilter made of polyethylene (PE) plastic. Normally PE biofilters are placed above ground level fitted with a sludge discharge valve for easy flushing and cleaning. The sludge water is lead to the waste water treatment system outside the aquaculture recirculation system. The picture on the right reveals the size of a large PE biofilter. Source: AKVA group.
Biofilter maintenance includes:
• Brush the top plate every second week to avoid bacteria and algae developing and eventually blocking the holes in the perforated top plate
• Brush and clean the microbubble diffusers in the process water pipe from last biofilter chamber to microparticle filter every second week
• Regular monitoring and cleaning schedule
Figure 5.6 The flow pattern in the shown multi chamber PE biofilter goes from left to right and upstream in each chamber. Most of the organic material is removed by heterotrophic bacteria in the first chamber. The consequent low organic load in the latter chambers secures a thin nitrifying biofilm for converting ammonia to nitrate. The last chamber is called a microparticle filter and is designed for removal of very fine particles that have not been removed by the mechanical filter. Source: AKVA group.
The following parameters should be checked regularly:
• Check the distribution of air bubbles across each of the biofilter cham- bers. Over time the biofilter will accumulate organic matter, which will impact the distribution of air bubbles and increase the size of the bubbles
• Check the height between the water surface level in the biofilter and the PE cylinder wall top edge to identify flow changes through the biofilter and microparticle filter
• Regularly measure the water quality parameters that have most relevance to the biofilter
• Closely monitor the remaining volume of base or acid used for dosing.
Cleaning and flushing for sludge removal in biofilter
A mix of inorganic material, dislodged biofilms and other organic matter that is difficult to break down by the microorganisms may accumulate below the biofilter. This should be removed by the sludge removal system placed in the chambers.
For sludge removal flush follow the protocol below:
• Bypass the PE biofilter that is to be cleaned
• Open outlet discharge valve for few seconds (approx. 10 sec.)
• If sludge pump is installed: Pump the sludge from PE biofilter and check for a brown coloration in the water
• Continue this procedure for all biofilters and microparticle filters (and turn off the sludge when finished). Ensure there is no siphoning from the biofilter chambers via the sludge pump. If there is a possibility of losing water this way, shut all the outlet discharge valves.
Simple cleaning of biofilter using air
Twice a week it is recommended to apply a simple cleaning protocol. In this procedure the PE biofilters are cleaned by air.
For simple biofilter clean follow the protocol below:
• Do not change the flow to the biofilter
• Open the air cleaning valves on the first PE biofilter
• Check with that the cleaning blower is ready for operation. Turn this blower on
• Direct all cleaning air to biofilter 1 for 10-15 minutes. The process water flow through the biofilter will transfer the loosened organic materials to the following chamber
• Direct all cleaning air to the next PE biofilter for 10-15 minutes. Con- tinue the procedure through to the last biofilter. Exclude the micropar- ticle filter
• All the loosened organic material finds its way to the microparticle filter.
Related news
Tools

Phối trộn thức ăn chăn nuôi

Pha dung dịch thủy canh

Định mức cho tôm ăn

Phối trộn phân bón NPK

Xác định tỷ lệ tôm sống

Chuyển đổi đơn vị phân bón

Xác định công suất sục khí

Chuyển đổi đơn vị tôm

Tính diện tích nhà kính

Tính thể tích ao