Hyper-drive: the pros and cons of intensive RAS production in the US
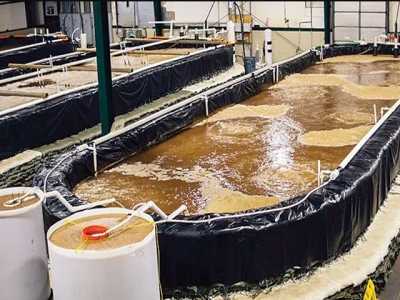
The hyper-intensive production of tropical species might be a hard sell in the US, but a handful of companies have developed systems that have made successful leaps in the sector.
Florida Organic Aquaculture produced vannamei shrimp in biofloc raceways
Over the past 20 years there have been several well-funded attempts at hyper-intensive commercial shrimp farming in the US. Two of these established “high tech” farms were destroyed by hurricanes during the years 2017 and 2018 and one was reported to be unable to recover. A third established intensive shrimp farm that had obtained over $20 million in funding is now defunct, apparently due to an inability to continually produce shrimp for market at an economically sustainable level.
However, there are three examples of successful hyper-intensive commercial aquaculture operations in the US that we can use for important comparisons. Blue Ridge Aquaculture of Virginia grows tilapia hyper-intensively. The farm is located outside of the influence of hurricanes and has been economically viable for over 25 years. The Fish Site has previously reported on this company, who told us that total vertical integration and firm biosecurity are the keys to their success. Blue Ridge currently grows 4 million pounds of tilapia per year and ships them live to market in big cities. This is one way that an intensively farmed US aquaculture product can successfully compete with cheap Asian seafood imports, which currently dominate the US market.
Another important example comes from a US producer of shrimp that uses zero water exchange recirculation technology, which has operated for the past six years. The company, American Mariculture – which operates under the Sun Shrimp brand – is located on Pine Island off the coast of Florida and produces 327 tons of 25g shrimp per year. The shrimp are sold fresh, never frozen, from their website; they are then distributed throughout the US directly to restaurants using overnight UPS shipping.
Although Sun Shrimp grows shrimp to a size just outside the commodity range, they have been successful in competing with cheaper imports. According to Robin Pearl who is the president of the company, “Marketing the shrimp has not been a problem—even at $13 a pound.” This is another way an intensive aquaculture production system employing tanks could be economically viable in the US: selling directly to retailers and restaurants is an impressive strategy considering these shrimp are sold at over three times the price of cheaper frozen imports.
A more recent success story comes courtesy of an integrated organic salmon and lettuce producer in Wisconsin. The company, Superior Fresh, just like American Mariculture, ships directly to market. Aquaponics is well known for its efficiency and typically generates at least 80 percent of revenue from plant harvests produced from fish waste – as confirmed by chief operations officer Brandon Gottsacker who says (in regard to growing lettuce from the waste produced by salmon which has an FCR of 1:1): “That’s 1lb of input into the system and 10lb of healthy organic food out of the system.” Most importantly, such systems rely on adequate solids removal and perfect control of ion concentrations imperative to growth of vegetation in water. Superior Fresh sells 100,000lb of leafy greens every month. Producing fresh organic produce in an area known for its long, cold winters is another way to successfully compete with cheaper agriculture imports.
It is well known in the shrimp farming sector that industrialised countries such as Australia and the United States have very low output because they cannot compete economically with such industry giants as China by growing a commodity-size shrimp of 15-20g. Growing smaller shrimp allows a faster turnover promoting a high profit potential, higher growth rates and a growing season of two to three months that fits in well with countries like China that experience periodic, challenging dry and wet seasons.
Moreover, subsidies and financial incentives provided by the government of China, as well as a high seafood demand, cheap labour, lack of environmental regulation and lower land costs, have resulted in China’s success in shrimp aquaculture. Therefore modern intensive shrimp companies in the US have attempted to escape the commodity market by growing shrimp greater than 25g. However, growing larger shrimp at a high biomass is more challenging due to longer growing seasons which involve a greater risk of loss of shrimp due to disease, periodic devastating weather events, water-quality issues and slower growth rates.
There are a few published economic analyses of intensive shrimp farming that discuss the important variables and minimum production numbers that are required for success. One of the few complete bio-economic analyses conducted on indoor greenhouse culture of shrimp was developed by Van Wyk et al in 1999 using raceways. After a series of research production trials, a hypothetical model of a commercial farm was developed. Using the actual research data, an internal rate of return (IRR) of 13 percent was calculated using the poor production performance of shrimp growing at a low 60 percent survival, 0.7g per week and a harvest biomass of 2.5kg/m3. The authors of this study suggested that if survival alone could be increased to a moderate rate of 70 percent, then the IRR would increase from an unattractive 13 percent to a viable rate of 26 percent, indicating the economic sensitivity of this variable.
Alternatively, if the low growth rate of 0.7g per week could be slightly increased to 0.85g per week, then the IRR would increase from 13 percent to a healthy 32 percent, exposing another economically sensitive variable. If both survival at 70 percent and growth at 0.85g per week are considered, the IRR of this model jumps to 48 percent, making it a very attractive investment opportunity. However, the analysis considers a premium market price of $5.86 per pound at an 18g size for the year 2001, which is nearly twice what Van Wyk et al. had previously estimated during that period.
Sun Shrimp produces 325 tons of organic shrimp a year
These results were confirmed by a second and much more recent intensive-aquaculture production analysis in 2009 (Hanson et al.). By increasing survival in their economic models by 20 percent, the IRR was increased to 97 percent. Furthermore, a 20 percent increase in stocking densities or growth rate increased the net present value (NVP) by 57 and 45 percent. Contrary to this, a reduction of 20 percent in the cost of feed or post-larvae only reduced the NPV by 22 and 9 percent. On these results, it seems obvious that for an intensive-aquaculture project to be commercially successful, survival and growth rates have to be maximised.
Current attempts at commercial hyper-intensive shrimp production systems in the US have reported regular harvest biomass from 2.2kg/m3 to 3.5kg/m3 of shrimp larger than 30g. The production costs reported were $9.35 per kilogram, with a sale price of whole shrimp established at $12.6 per kilogram. Incorporating the fixed costs for the necessary expensive infrastructure associated with hyper intensive shrimp aquaculture would result in little or no profit per kilogram of shrimp produced. Therefore there is a clear need to increase harvest biomass by increasing shrimp survivals and also to develop alternative markets in order to provide economic sustainability for hyper-intensive shrimp production in the US.
In conclusion, hyper-intensive aquaculture operations would be more sustainable if they were located out of the range of devastating seasonal weather events. In addition, the ability to produce products that are outside of the influence of the commodity market, including niche markets, would be imperative for financial success. The most important production variables that have been outlined in published studies indicate that high growth rates and high stocking numbers with good survival numbers would be necessary to achieve the high biomass and efficiency that intensive aquaculture operations in the US require for sustainability.
Related news
Tools

Phối trộn thức ăn chăn nuôi

Pha dung dịch thủy canh

Định mức cho tôm ăn

Phối trộn phân bón NPK

Xác định tỷ lệ tôm sống

Chuyển đổi đơn vị phân bón

Xác định công suất sục khí

Chuyển đổi đơn vị tôm

Tính diện tích nhà kính

Tính thể tích ao