Expert Q&A: How to design offshore aquaculture pens
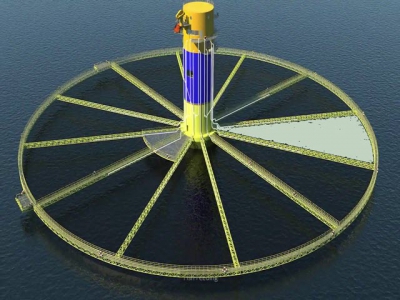
FUZHOU, China -- Behind arguably one of the most ambitious projects in aquaculture underway in China is offshore oil and gas services firm De Maas. Headquartered in Qingdao, China, over the past four years De Maas has had a team of engineers steeped in the world of deep sea oil wells and offshore rigs turn their skills and experience to designing huge offshore pens for farming fish.
Last summer, De Maas signed a deal with a consortium of firms in Fujian province to build five such pens in a project worth $150 million. In early June, Undercurrent News visited the shipyard in Fujian where De Maas is overseeing construction of the first pen. There, and in previous conversations, the De Maas team explained the challenges of designing and building an offshore pen – and what to expect when a typhoon hits.
Below is an edited and combined version of the interviews.
Undercurrent News: What elements of offshore rigs for the oil and gas industry have you taken in your design of your deepwater aquaculture pens?
Phillip Schreven, co-founder and director of De Maas: You can use offshore technology from oil and gas industry to design these things. But there are some very specific and typical issues about aquaculture that you have to take into account.
Essentially, unlike an oil or drilling rig, you're not supporting anything -- you're just keeping fish together. So the focus might be on reducing weight while still having a large volume and being able to go through a typhoon. While keeping weight down is sometimes a challenge in offshore oil and gas, it is not as critical as it is for an offshore aquaculture system.
Andrew Lipman, greater China region area operations manager at ABS: This project takes a lot from the offshore oil and gas industry. In the oil and gas industry what supports the production going on from the seabed, such as pipelines, to the floating platforms, is called the spar. The spar is a very proven design – it’s been used for at least 30 years.
UCN: Fujian is very typhoon-prone. Did you design the pens specifically for the seas near Fujian?
PS: We did not design this thing specifically for China, but we did design it specifically for offshore use.
De Maas pens. Credit: De Maas
Rather than having to put the offshore farm in a sheltered area with the troubles to sustainability and quality that go with that, we said, okay, if you want to market and sell these units worldwide, we have to make sure that it can truly withstand harsh environments and exposed areas. Not every country has a coastline with some islands where you can hide behind.
If you look at some of these offshore farms they're usually situated leeway of an island, that means downwind of an island. So they still have some protection from the island form wind and waves.
But not everywhere has such natural protection. If you go through a typhoon in Southeast Asia, you get into some difficult conditions. Same with the North Sea. So it was tailored specifically for those sort of conditions.
AL: I can tell you I have been out in a typhoon in the South China Sea. It’s quite an experience. You have an oil rig in the middle of these winds which can be over 200 kilometers an hour. And obviously, they come through with no damage.
UCN: Compared with designing a huge offshore oil rig designing a pen to hold fish looks very straightforward, though. Is that the case?
PS: No, not really. You want a large, controlled volume, but you want this volume at the lowest cost. That's something you don't meet in oil and gas very often. In the oil and gas industry margins are much larger, making the cost of material (steel mainly), less critical. For farmers that's not the case, they operate on thin margins. But they still need it to go through all these storms.
AL: I'd call this a high-tech project. I mean, there’s nothing simple about it. It's not just putting a net somewhere.
UCN: So how are you designing the pen to withstand a typhoon?
PS: Part of the solution is to submerge the pen. If you go down 2x to 3x below the wave height, then in any given circumstance the wave effect dies out. It works very effectively and you can calculate that.
De Maas pen submerged during bad weather. Credit: De Maas
So when the really bad weather comes in, you move out of this turbulent area, also called the wave zone, into a much calmer area, and just wait there. Subsea feeding systems can also be fitted so fish can still be fed.
If you stay in the wave zone during a storm, whatever you put there is going to have to be very strong, otherwise it's going to break and sink. That’s one reason why some of our competitor's pens are so heavy; they have to be because the entire thing stays in the wave zone at all times. It needs a lot of steel so that it comes through a big storm undamaged.
AL: Another thing you can do is you can take what is called the sail area [the area wind pushes against] and you reduce that.
UCN: So your main aim is to reduce weight and ensure the pen maintains its structural integrity or doesn’t sink?
PS: That’s correct. If you use our competitor's farm for farming golden pompano, or yellow croaker, it's not viable. Even with our farms sometimes people are making an issue about the cost.
Construction of De Maas’ offshore aquaculture pen in Mawei
The cost of these farms should be such that worldwide people can move farther from shore. If you want to farm certain fish offshore in Africa, then you need to reduce the amount of steel you use.
So the issue is how to reduce costs. Certain equipment you need in all cases -- like pumps and feeding systems -- becomes bigger as you go offshore. Those costs you can account for by farming more fish. There's not much to tweak there. But in terms of the design, there are things you can do.
UCN: Does that mean the SalMar pen was badly designed?
PS: No. It's an absolutely safe and reliable design that one can expect from their designer, Global Maritime. They are a very reputable engineering company with a long and successful track record. I think with their design they came up with an answer to what SalMar wanted. Designs are usually made within the constraints of a client's requests. We started out from a different, more basic point.
But if your first step is to design something that stays within the wave zone, then ultimately you're going to pay a price for that decision. Cost is where the challenge is in developing offshore aquaculture worldwide.
UCN: Can you tell us a little bit more about the design then?
Ma Kun, project manager at De Maas: The pen is 140 meters in diameter and the net is 12m high. The pen has a floater which is below the surface and which is fused to the central spar. Water can be pumped into the floater to make the pen sink, and then pumped out to make it rise again. The spar houses the control room for the pen.
The pen is welded together from 52 separate modules.
UCN: Where does the pen get its power supply from? Is there a generator on the pen?
PS: The first unit will get its power from two onboard Caterpillar gensets (diesel) and solar panels on top of the unit. The solar panels provide power to things like lighting and bridge equipment. Apart from serving as emergency power, the Caterpillars assist in powering the feeding system the largest consumer, the ballast pumps. The latter require most power when resurfacing from storm draft.
Pen being re-supplied. Credit: De Maas
For the following units, we are integrating wave power technology to increase the sustainability of the system as a whole. Wave power technology is being tested and it looks to be a good match with the SSFF technology. A small-sized diesel generator may still be fitted to serve as emergency power as per Class (ABS) requirements.
UCN: How long will it take to build?
MK: It will take about six months from the start of construction. The busiest phase at the shipyard will be when we start to fit the blocks together.
UCN: Are the steel components pre-fabricated before arriving at Mawei?
AL: No, all the steel is purchased either in plate or shaped forms by Mawei. Then it's formed and welded into shape. So it's basically from scratch. That's their specialty.
MK: Some parts are hammered into shape with a large hammer. Other parts are molded into shape with a press.
UCN: How will it be delivered to the location once it is completed?
Carol Shang, sales manager, De Maas: From a designer's point of view, you can wet tow it, you put it in the water, or dry tow it, where it's on a barge or vessel, and transport it to the final location. It depends on the depth of the water and location where it'll be installed. It will be coordinated with client and yard.
Ours can be assembled at the location too. So if somebody orders from New Zealand it can be transported in blocks and then assembled there, providing the opportunity to create local content as well.
PS: The transport of an entirely completed farm is hugely expensive. The trip from Asia to Norway would have cost anywhere between $7-10 million. It's hardly sustainable if cost of the unit isn't controlled.
UCN: I understand ABS plays a crucial role in the project. Could you explain what this is?
AL: ABS is a classification company. When a company like De Maas proposes a new design, there has to be an engineering organization which reviews the design to international standards. ABS is that organization.
Smolt transfer into the pen. Credit: De Maas
So a designer’s plans will all need to be reviewed to ABS standards, which are recognized worldwide. This includes statutory agencies like China MSA, China Coast Guard, US Coast Guard -- they would recognize our ability to approve plans. So that's the first step.
Next, you start steel work and construction. During construction you have certain standards; welding standards, quality standards. We need to know, are they being observed by the shipyard? The owners are interested in that, as well as the classifications society. We have people stationed in the shipyard observing the qualification of the personnel tested to our standards.
Then once the project is ready to be installed, it's very important that it stays where it's supposed to be, because if a storm comes, you don't want it to drift away. So how is it installed? What's the engineering design? The strength of the mooring system is very important and has got to be designed to a certain level. Then it’s got to be installed as per the design.
And then as the years go by, you're doing life cycle maintenance on the project. So this is 30-35 year lifespan. Every year it will be checked by our personnel, our inspectors.
UCN: Are there international standards for offshore projects like this?
For sure there are standards. And they come in big, thick books. All the materials, the generators, the pumps, all that comes from a supplier, usually in China, all that is tested to our standards. And at those factories, our personnel will test the equipment.
Feed being transferred into feed silo. Credit: De Maas
You need to also look into subcontractors -- what's their background? Do they have ISO9000 certification? If Mawei [shipyard] brings in a third-party welding company -- who's tested those welders?
The structure [of a rig] over the years has evolved, and the rules that are written to certain things like welding standards, metal types, metal thicknesses, these evolved over time. It wasn't just somebody sat down and designed it one day and said here you go.
UCN: Do different countries have different standards? What are the standards requirements in China like?
Yes and no. It’s not governmental. It's a third party. But it's not only ABS. DNV is the Norwegian standard. LR, British standards; ABS, American. Each have their own rules. There are differences; I don't want to say ours are better. Just different.
But in offshore, ABS is the biggest. In shipbuilding we’re not the biggest.
UCN: And are there standards for offshore aquaculture pens?
ABS now is coming out with our specific aquaculture guide for structural, addresses, rules we have developed. The new rules we're going to be publishing in September/October will be addressing this issue. They will be very specific to the aquaculture sector. So, they’ll be about what the structural requirements are. Over-design could be as bad as under-design.
Currently it’s at the stage of industry comment. We've already drafted the rules and they're out to people like Philip and Mark, and some others, people with interests in the industry. We’ll then come back and take those comments into the account. We have teams in both China and Houston involved in this.
UCN: How will ABS standards for offshore aquaculture pens help the industry?
AL: It will make it much easier for people to build these things, 100%. It will be very specific to them and make it easier when they have the guidance in front of them at the design stage.
Fish inside the pen. Credit: De Maas
Unfortunately, it wasn't ready when De Maas was conceiving their design. We weren’t as proactive then. But because of a history of working together in oil and gas, we quickly found each other in recognizing the need to apply the ABS offshore standards in the absence of specific statutory requirements for offshore farms.
Designers will still have freedom to make whatever design they need to do. It will just be for designers to know certain strength calculations and equipment that's universal.
But to develop a manual is a lot of work. Many engineers spent a lot of time on it, 40 hours a week for one month, two months, three months. To write the rules in hours, I’d say it would take 1,500 - 2,000 hours.
UCN: Do you see offshore farms developing and getting better over time then?
PS: Actually, we already have ideas for how to upgrade it. You can compare it to iPhone upgrades. I'm quite sure that farm number ten will be quite different from what we are doing today.
Có thể bạn quan tâm
Phần mềm

Phối trộn thức ăn chăn nuôi

Pha dung dịch thủy canh

Định mức cho tôm ăn

Phối trộn phân bón NPK

Xác định tỷ lệ tôm sống

Chuyển đổi đơn vị phân bón

Xác định công suất sục khí

Chuyển đổi đơn vị tôm

Tính diện tích nhà kính

Tính thể tích ao hồ